The world's leading medical device development company has turned to Ming-Ren to unlock the advantages of digital manufacturing models. From connected devices to large-scale personalization of medical products, digital manufacturing accelerates development and market introduction through rapid prototyping, bridging tools, and small batch production.
Why do medical device development companies use Mingren?
Analysis of Interactive Design
Significant design adjustments are made to the manufacturability (DFM) design of each quote to save development time and cost.
Small batch production
To simplify your supply chain, you can obtain small batches of parts as soon as 1 day before and after the product is launched.
Bridge tools before production
Design and market validation of reasonably priced bridge tools prior to capital investment in the tools.
Technical agnosticism
Multiple manufacturing techniques across four services mean that no matter what your project needs, parts can be paired with the right equipment and processes.
Medical material
Choose from high-temperature plastics, medical-grade silicone rubber, 3D-printed micro-resolution and micro-fluid parts, and hundreds of other plastics, metals and elastomers.
Rapid prototyping
Create prototypes in production-grade materials for functional and regulatory tests, or preview 3D-printed models and organ scans before medical procedures.
Which material is most suitable for medical applications?
The high temperature plasticPEEK and PEI (Ultem) are high temperature resistant, creep resistant and suitable for applications requiring sterilization.
Medical grade silicone rubberDow Corning's QP1-250 offers excellent thermal, chemical and electrical resistance. It is also biocompatible and can therefore be used in applications requiring skin contact.
Carbon RPU and FPU Carbon DLS USES rigid and semi-rigid polyurethane materials to make functional parts, ideal for late prototyping or end-use equipment.
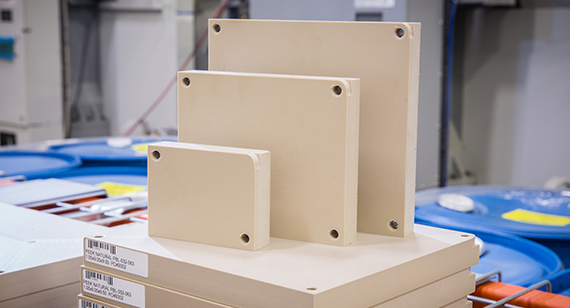
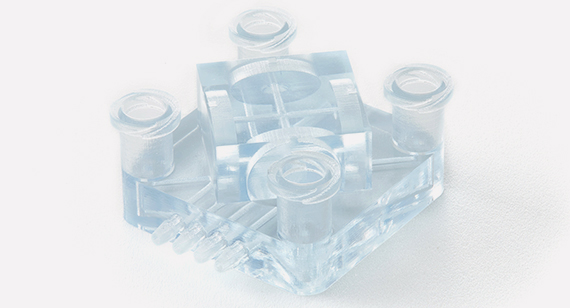
Microscopic resolutionMicroFine™ (green and gray) is a proprietary material developed for building complex 3D-printed parts as small as 0.0025 inches.
microfluidic The Watershed (similar to ABS) and Accura 60 (similar to PC) are transparent materials that can be used for microfluid components and transparent components, such as lenses and housings.
Medical alloyBetween machined and 3D-printed metals and sheet metal, more than 20 metallic materials are available for use in medical components, instrumentation, and other applications. Metals such as titanium and inconel are temperature-resistant, while various stainless steel materials have corrosion resistance and strength.
Common medical applications |
---|
Our services and processes have multiple functions to meet the needs of the healthcare industry. Some common applications include:
|